In an era where precision and reliability define industrial success, the demand for cutting-edge motion control and testing solutions has never been higher. From automotive giants to renewable energy pioneers, industries worldwide are turning to hysteresis-based technologies and motor test systems to push boundaries. Let’s explore how these innovations are reshaping engineering excellence.
---
**Hysteresis Brakes: Silent Guardians of Precision**
Imagine a braking system that operates without physical contact, eliminating wear and tear while delivering consistent torque. Energy-efficient automation achieve exactly this. By leveraging Appliance motor noise testing , these devices provide smooth, vibration-free braking—ideal for applications requiring delicate control, such as medical robotics or semiconductor manufacturing.
Why engineers love them:
- Zero maintenance due to non-contact operation
- Exceptional torque consistency across speeds
- Silent performance in noise-sensitive environments
- Customizable designs for aerospace to textile machinery
A leading electric vehicle manufacturer recently integrated hysteresis brakes into their assembly line robots, reducing maintenance downtime by 40% while improving positioning accuracy.
---
**⚡ Hysteresis Dynamometers: The Truth-Tellers of Torque**
When every Newton-meter counts, hysteresis dynamometers emerge as the gold standard for torque measurement. https://meadows-moser-2.hubstack.net/powering-precision-discover-the-future-of-hysteresis-brakes-dynamometers-and-motor-testing-solutions-1743315676 excel in testing high-speed motors and turbines, offering:
- Real-time load simulation up to 15,000 RPM
- Instantaneous torque adjustment capabilities
- Energy recovery systems for sustainable testing
- Compact footprints for lab and field use
A wind turbine developer utilized hysteresis dynamometers to validate their new 5MW generator design, cutting prototype testing time from 12 weeks to 18 days while capturing 92% of test energy for reuse.
---
**🔩 Hysteresis Clutches: Where Precision Meets Power**
Modern manufacturing demands clutch systems that can handle rapid cycling without degradation. Hysteresis clutches answer this call with:
- Slip-free power transmission
- Microsecond-level engagement precision
- Built-in overload protection
- Compatibility with IoT-enabled predictive maintenance
An automated packaging line upgraded to hysteresis clutches reported a 67% reduction in product misalignment errors and 30% longer mean time between failures.
---
**Motor Dynamometers: The Fitness Trackers for Electric Machines**
Just as athletes need performance metrics, motors require rigorous testing. Modern motor dynamometers serve as comprehensive diagnostic hubs, offering:
- Bi-directional power analysis (up to 98.5% accuracy)
- Thermal mapping for cooling system optimization
- NVH (Noise, Vibration, Harshness) profiling
- Automated test sequences compliant with ISO 17025
A drone propulsion manufacturer implemented advanced motor dynamometers to achieve 99.7% batch consistency, securing a crucial aerospace certification.
---
**🔋 Motor Test Equipment: Building Tomorrow’s Electrified World**
From e-mobility to smart factories, next-gen motor test solutions are enabling breakthroughs:
- 4-quadrant testing for regenerative systems
- AI-powered fault pattern recognition
- Cloud-based data correlation across global teams
- Modular designs scaling from micro-motors to 10MW industrial drives
A recent case study revealed how an EV motor factory reduced end-of-line test duration by 54% using adaptive test equipment with machine learning algorithms.
---
**Motor Test Systems: The Neural Network of Quality Assurance**
Integrated test ecosystems are becoming the backbone of smart manufacturing:
- Digital twin synchronization for virtual-physical testing
- Edge computing for real-time quality gates
- Blockchain-secured test records
- AR-guided maintenance and calibration
When a robotics company implemented a full motor test system, they achieved 360-degree traceability, decreasing warranty claims by 28% in the first quarter.
---
**The Sustainability Edge**
Modern hysteresis and testing solutions contribute to greener operations:
- Energy recovery systems reducing test facility consumption by up to 80%
- Material efficiency through extended component lifetimes
- Data-driven designs minimizing prototype waste
- Compliance with emerging circular economy standards
---
**Choosing Your Innovation Partner**
When selecting motion control and testing solutions, prioritize providers offering:
1. Cross-industry application expertise
2. Custom engineering support
3. Future-ready upgradability paths
4. Global service networks
5. Cybersecurity-certified data systems
---
**The Road Ahead**
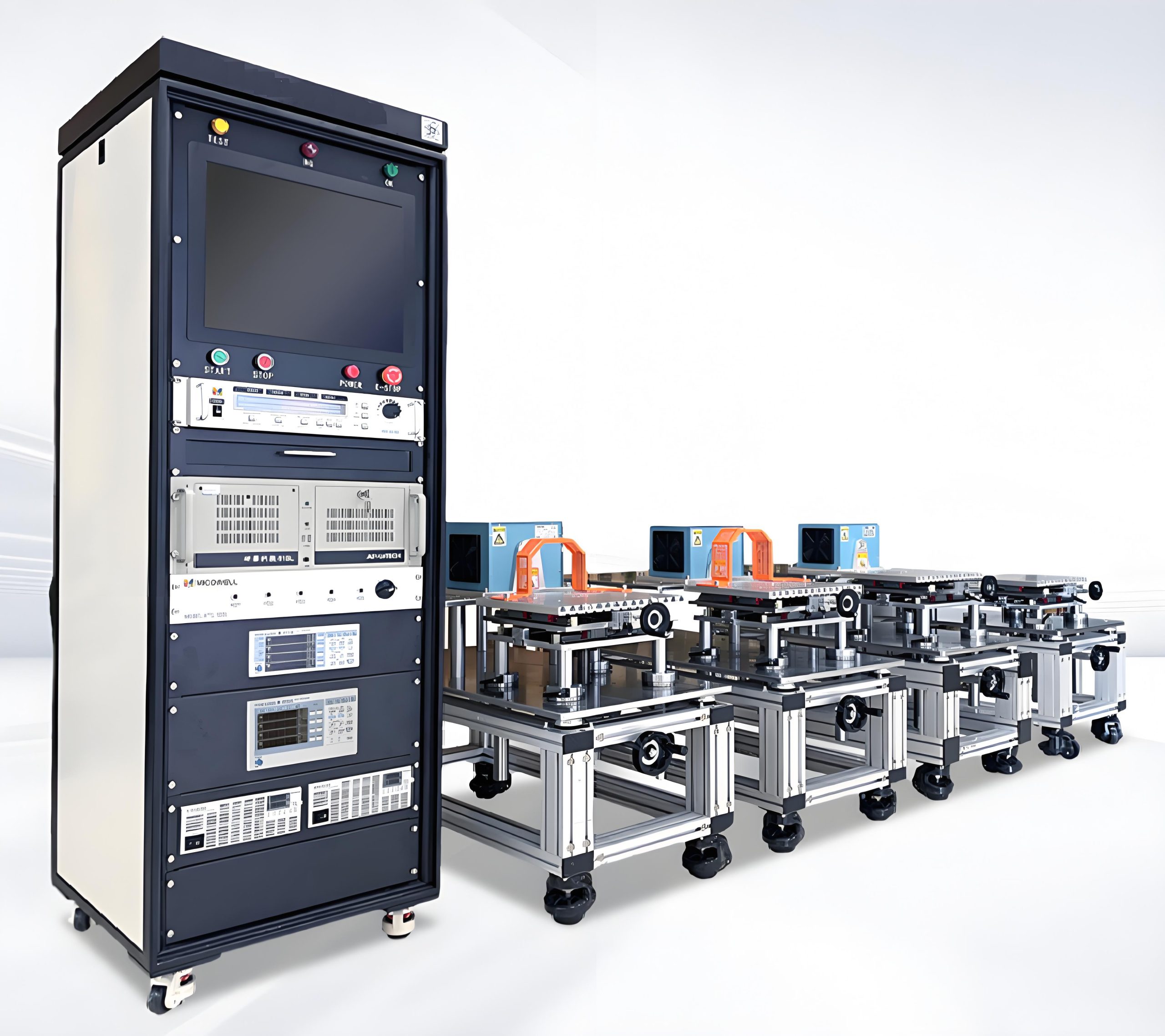
As industries accelerate toward electrification and Industry 5.0, hysteresis technologies and intelligent test systems will play pivotal roles in:
- Enabling megawatt-class wireless power transfer
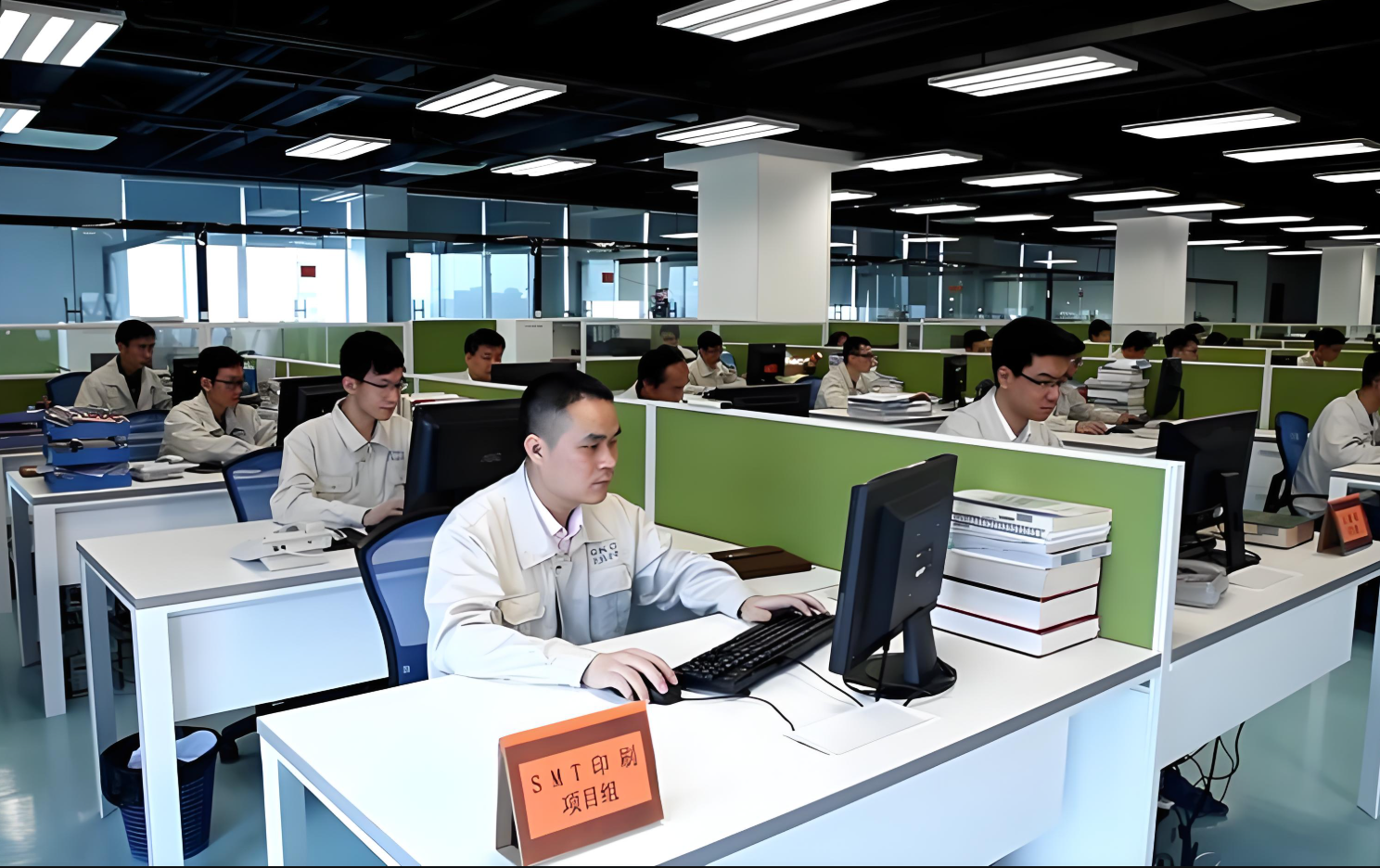
- Facilitating hyper-fast motor prototyping cycles
- Supporting AI-optimized mechanical designs
- Powering next-gen space exploration tech
---
Whether you’re optimizing existing systems or pioneering breakthrough technologies, the synergy between advanced hysteresis devices and smart motor test solutions creates a foundation for unprecedented engineering achievements. The question isn’t whether to adopt these technologies—it’s how quickly you can implement them to stay ahead in the race for technological leadership.
[End of Article]